By Lambert Strether of Corrente.
THIRD YORKSHIREMAN: … There were a hundred and fifty of us living in t’ shoebox in t’ middle o’ road.
FIRST YORKSHIREMAN: Cardboard box?
THIRD YORKSHIREMAN: Aye.
FIRST YORKSHIREMAN: You were lucky. We lived for three months in a paper bag in a septic tank.
–Monty Python’s Flying Circus, Four Yorkshireman
Chapter three of Snow Crash, Neal Stephenson’s libertarian udystopia, opens like this:
Hiro Protagonist and Vitaly Chernobyl, roommates, are chilling out in their home, a spacious 20-by-30 in a U-Stor-It in Inglewood, California. The room has a concrete slab floor, corrugated steel walls separating it from the neighboring units, and – this is a mark of distinction and luxury – a roll-up steel door that faces northwest, giving them a few red rays at times like this, when the sun is setting over LAX. …
But there are worse places to live. There are much worse places right here in this U-Stor-It. Only the big units like this one have their own doors. Most of them are accessed via a communal loading dock that leads to a maze of wide corrugated-steel hallways and freight elevators. These are slum housing, 5-by-10s and 10-by-10s where Yanoama tribespersons cook beans and parboil fistfuls of coca leaves over heaps of burning lottery tickets..
It is whispered that in the old days, when the U-Stor-It was actually used for its intended purpose (namely, providing cheap extra storage space to Californians with too many material goods), certain entrepreneurs came to the front office, rented out 10-by-10s using fake IDs, filled them up with steel drums full of toxic chemical waste, and then abandoned them, leaving the problem for the U-Stor-It Corporation to handle.
But didn’t Stephenson go just a little meta, here? Rather than putting Hiro Protagonist [nudge] in an steel box at the decaying end of the supply chain, why not move the housing question back up the chain closer to the beginning?[1] Why not, in other words, a shipping container? Especially if your shipping container residence looks like this:
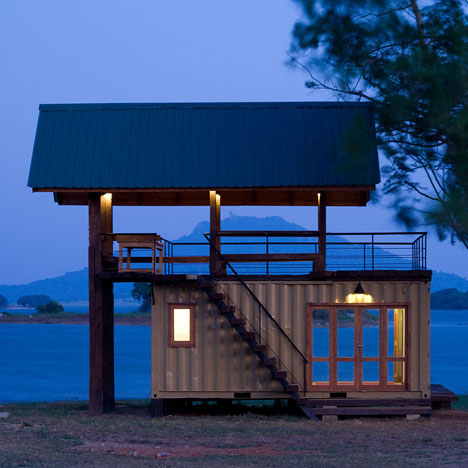
There are many other photos of bigger, more luxurious shipping container homes where that one came from; here’s another set. However, it wasn’t luxury that seized my imagination; it was cost.
However, additional advantages will spring to the mind of NC readers, in “A person’s home is their castle, and vice versa” mode; a big steel box seems less vulnerable to infrared inspection by our increasingly officious national security state; not to mention less vulnerable to projectiles of all sorts. (Of course, as the owner opens holes in the box for light and air, water, and power, these advantages decrease, but no doubt that can be mitigated; slit windows, for example, as in medieval castles.) And while a conventional, stick built house is assaulted along many dimensions — I worry about the weight of snow on the roof, ice at the foundations, critters under the house, hurricanes, shifting foundations, the general tendency of wood to rot or get eaten, and many other things — a steel box is really vulnerable along one: Rust. And the Cor-Ten steel used to manufacture shipping containers is a “weathering steel,” designed to resist rust by developing a protective oxide film. (Lots of solid technical detail at this site.)
Take this one from Australia:
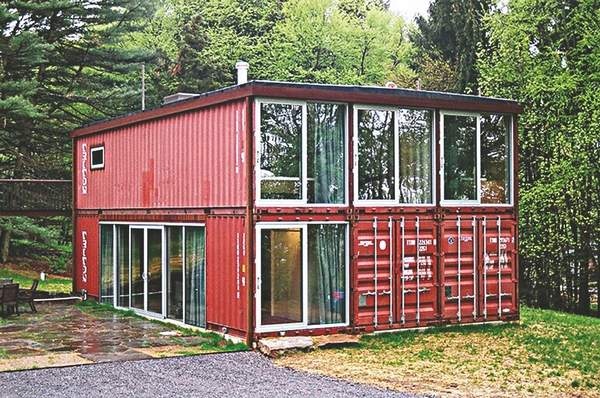
Or this even more utilitarian example:
I’m deliberately picking small and utilitarian images, because many other examples seem over-architected and more than a little twee, to me; if you want to go all House and Garden, why start with a shipping container in the first place? For example:
I love the roof garden, and I imagine it’s cooling, and I assume however the plants are watered doesn’t rust out the roof. Nevertheless, you know it was architected, because the first thought was to put in plate glass windows. So where’s my protection from surveillance and gunfire? Not that I’m foily.
But, as I said: What caught my eye was cost. To start a shipping container home, all you need is $2,000 for the container. And I’m the kind of person who finds comfort in having mentally handled the worst case scenario, and it seems to me that if, for whatever reason, I lost my home, or had to leave the country and start over, that I could scrape together enough for shelter and start over. That’s re-assuring!
Like that guy who lives year-round in a tent in Pownal, Maine: If he set up his tent in a shipping container, he wouldn’t have to get up every hour to brush off the snow! $2,000 seems a small price to pay for a good night’s sleep, every night, through the winters, plural.
And put a garden on the root, a permaculture garden round the container, start with some fruit and nut trees this time…
So perhaps I’m nourishing a fantasy of escape. On the other hand, there are plenty of people in Maine who escaped in just that way! Of course, if I wanted to live in the container, as opposed to living in a tent in the container, I’d need to think about insulation. Because every Mainer thinks about insulation! From a very useful FAQ at Residential Shipping Container Primer:
Q- Aren’t shipping containers just hot ovens [We can see this guy is not from Maine] when they are used for homes or offices?
A- Absolutely not! Sure, if you don’t know what you’re doing and don’t insulate. The reality is, that the new Ceramic spray insulation is most effective when applied to metal. In fact, if you build a home, office, emergency shelter or storage unitusing Ceramic Insulation paint (spray) the structure will probably be more energy efficient than a conventional home.
And from the same FAQ, the larger case for the container:
Q- Why promote Containers for home and office construction?
A- Shipping container modules are the most logical structure base for multiple reasons.
-Strongest structure. Stronger than wood, concrete, and even stronger than normal steel buildings.
-Lower cost per square foot than other base structures.
-They are truly Eco-Green structures: they are 85% recycled steel, and fully recyclable if demolished.
-Energy Efficiently because the metal is so cohesive to the Ceramic Insulation paints they are #1 in energy efficiency.
-Their use reduces the extreme surplus of Shipping Containers being stored near our harbors, ports, beaches and even inland cities.
And now, for fairness — and hedging in case I’m entirely driven by fantasy, here — let me quote the opposing case, from a shipping container home builder and owner, which I recommend you read in its entirety, including the comments, if you’re thinking about this. Here is the conclusion from “Tin Can Cabin”:
I’m not telling anyone they shouldn’t build with shipping containers, just that they should truly assess their reasons for doing it before they proceed. A shipping container cabin can be comfortable, secure, and aesthetically pleasing, but it will cost you considerably more than a conventionally built cabin. It’s not that different than wanting to build a log cabin – my true dream cabin, by the way. Log cabins also cost more per square foot than conventional construction, but somehow they seem like a better aesthetic deal to me.
In summary, I don’t regret my decision to build with containers. The peace of mind when I lock up my cabin is priceless – well, at least $15K worth.
That is, the author, who knows how to build both conventionally and with shipping containers, paid $15K more to do it the container way, instead of buildng a conventional cabin. Read the article for the complete detail, but here’s the basic principle:
You also have to consider that a shipping container shell still needs to be framed inside for attaching wallboard or paneling. This essentially turns the shipping container into very expensive siding if you don’t need its security.
In other words, the more conventional amenities you add, the more conventional construction wins out; and I consider things like plumbing and electricity necessary, and your typical plumber or electrician is going to be used to working with conventional, stick-built houses, and so it’s going to cost more to do it your way, instead of theirs.
So that’s a quick round-up on the seductions advantages and harsh realities disadvantages of shipping container homes. If you, readers, are thinking about building a shipping container home, or have built one, and want to share your experiences, or you decided not to, and want to share your reasoning, we’d love to hear from you in comments.
Concluding, I’d like to dolly back from the structural aspects of shipping container homes, and speculate a little on the macro-economic effects. This is dangerous, since I know virtually nothing about the housing market! First, I’ll talk about modularity; then, I’ll talk about demand destruction. Here again, readers, I hope you’ll expand on these ideas, especially those of you who are more knowledgeable than I am, i.e., almost all of you!
So, first, modularity. There’s an ISO standard for shipping containers; they’re completely modular. That’s why any one container can be stacked on any other, any crane can handle any container, and so on and so forth. Shipping containers destroyed the “break bulk” system of cargo handling where skilled longshoremen loaded cargo onto a ship much as you would pack randomly sized objects into a suitcase or the trunk of a car. Well, isn’t “stick built” construction just like “break bulk” cargo handling? Sure, two-by-fours are a standard size, and electrical sockets are standard, and Pemex plumbing is standard, but the dimensions of the housing structure itself are not standard. If they were, wouldn’t that enable modular “snap-in” components for water, electricity, and heat that are currently installed by hand? (And will some Chinese company figure that out, and become the Ikea of global home construction?) Tin Can Cabin says this:
Designing an efficient and liveable cabin in multiples of 8, 20, and 40 foot lengths is a huge limitation. Need an extra two feet on one end to fit your dream kitchen? It’s not going to happen without taking something away from an existing space. The flexibility of frame construction to scale to virtually any size is a substantial benefit compared to container construction.
Well, what happens when people, en masse, decide that dream kitchen isn’t worth the extra two feet? Leading me to my second point:
Demand destruction. What if highly modular domestic architecture succeeds, and makes the dream kitsch go away? The marble countertop industry takes a hit; the stainless steel hood and fan industry takes a hit; fancy German appliances take a hit, and so on and so forth. The Tin Cabin alludes to demand destruction in extreme form:
I know I’m going to get comments like “I can build a container cabin for $20/sq foot” or “your cabin is overbuilt and too expensive”. Both of these comments are true if you don’t mind living in a shack more appropriate for a third world refugee camp [rather like Hiro Protagonist!]. I’ve seen shipping container “cabins” with no insulation, the wrong insulation, raw plywood flooring, no wallboard or paneling, no roof, no foundation, and no utilities. If all you want is a metal box lying on the ground….
That’s a lot of demand destruction!
… then yes, shipping container construction can be both easy and cheap.
Of course, “easy and cheap” is what I had in mind for my fantasy of escape, and I bet that’s what the guy in Pownal, Maine would want too.
But if we move up from the (rather over-wrought) “third world refugee camp” to “highly modular and much more simple,” what happens to aggregate demand? If housing and construction are key drivers of the economy, what happens to jobs and growth when you can snap a house together out of interchangeable parts in standard dimensions? Or, as we say, jawbs and groaf?
NOTE
[1] Apparently, the economics of globalization, with the United States as “the consumer of last resort,” enabled the growth of shipping container homes. Wikipedia:
The abundance and relative cheapness of these containers during the last decade comes from the deficit in manufactured goods coming from North America in the last two decades. These manufactured goods come to North America from Asia and, to a lesser extent, Europe, in containers that often have to be shipped back empty, or “deadhead”, at considerable expense. It is often cheaper to buy new containers in Asia than to ship old ones back. Therefore, new applications are sought for the used containers that have reached their North American destination.
I have some friends in central North Carolina who started their homestead together about a year and a half ago. They got a twenty-ish foot trailer for living in, which seemed quite comfortable, and then they used a cargo container to store their tools safe from the rain and animals. When they invited me over we climbed on top of the container and had beers on their ‘balcony’ overlooking their huge gardens and surrounding forests.
A different friend of mine bought a used trailer and lived in it very comfortably for ~$9k, I think, though I’ve heard the average cost can be $15k-$20k or more for fully outfitted, nice quarters.
I estimated my two friends in North Carolina paid ~$20k for the move-in-ready living quarters and storage, which seemed like a sweet deal for a couple itching to start permaculturing-up their homestead.
thanks, this has been an idea of ours for a while.
here is a show on a guy building with 4 containers
https://www.youtube.com/watch?v=2041kuJs1xw
Beautiful structure. At the same price per square meter at public housing–but the land was free. It would be interesting to do a comparison w/ land price included.
And no architect fee, how many hours did he put in to it? Was it al included, electricity, water, sewage, road to the site? How energy efficient is such structure, a thin layer of sprayed insulation in the corrugated steel. How was it heated? Just some electrical radiators or something more advanced, waterboarn in the floor. There dint seems to be any “green” touch to it, solar panels, heat pump or such.
Didn’t seems to be something for a Nordic climate, normally you sort have to put a thick “cardigan” on the construction to keep it warm and be careful to not get the dew point in the wrong place.
Very few homes are designed by architects. Only the well-to-do, or time free have a one-off home design. Tract homes may have seen some architects hand, but probably only for advertisement rendering. Many of the McMansions seen today are simple derivatives from a standard plan. Few have been designed in context with the surrounding landscape, advantageous solar orientation, or non-auto access.
That said, be on the lookout for the DOE Solar Decathlon 2015: selected colleges competing on a broad range of sustainability, constructability, innovation, and of course, useability.
A experienced structural engineer will be more useful, at least here architects don’t know much about engineering. Wonder if that architect consulted any engineer for the project? The reinforcing of the containers seemed to be a bit ad hoc.
I know something was horribly wrong in the pre-Crash housing boom when I read about the McMansions with styrofoam pediments covered with stucco (“Oh boy, can you get stucco!”). What a horrible misallocation of capital.
This comes up frequently as a topic within the community resilience group I’m part of. As in “how cool is this? Let’s do it!”
But when the details of actual implementation in the real world get going, it completely falls apart.
We have a number of skilled plumbers, electricians, roofers, et.al. who chime in, offering to do the necessary work for an opportunity to participate. Everybody gets all excited…
THEN… one of our members, usualy a county clerk of some sort, checks the codes & requirements for occupancy, and… we’re done.
Lambert, good on you for adding reality to the container housing fad!
When the long slow crash gets to just the right spot, at least we’ll be good to go on the process.
Meanwhile, we’re all about improving what shelter we already have, getting food growing, adding as many non-consumptive systems as possible.
Mz Carr;
You are absolutely right about the local code enforcement angle. Also remember that local code is often an unofficial “enforcer” for local power elites. That’s how gentrification is carried out. Container homes would be an example of counter gentrification. When things go all t—s up, then sheer volume of survival type projects, which mainly ignore local codes and dare the authorities to intervene, will prevail. (My Dad was a building inspector in South Florida for several years. I’ve seen this in action.)
Many towns in the NYC metro area, along with mandating 5 or 7 acre minimum lots, do not permit manufactured housing at all.
Even if they did, one is no longer allowed to experiment and make mistakes. Micromanagement is the watchword. The building code in our state runs hundreds of pages, and that’s without the National Electrical Code which is incorporated by reference. Like the IRS code, the full scope and interpretation of the building code cannot be mastered by any one person. It’s a complex legal document, not a ‘how to’ guide.
Basically one has to go to rural areas, and in addition possibly invoke a subterfuge such as calling it an agricultural building (under Freedom to Farm laws), or else putting it on a wheeled chassis (so that it is not permanent construction), to build a container house without massive state intervention and intrusion. Effectively there’s a ‘housing guild’ which protects the interests of (first and foremost) local governments and officials, and secondarily licensed contractors.
DIYers are no longer welcome in corpgov America, and probably belong on watchlists for their antisocial tendencies /sarc.
Comrade Jim;
You really should remove the /sarc you appended to your missive.
At the local level, ‘out of the box’ thinkers, which sometimes includes Bigg Boxx Store customers, can become the recipient of much ‘official’ scrutiny. (A small quibble; since the term ‘social’ still generally means the public at large, perhaps anti-corporate tendencies would be a better fit.)
Someone I know has undertaken renovations — including electrical and plumbing work that requires permits — using a competent but unlicensed foreign national to do the work (heavily patronizing the orange box store nearby, and sometimes the blue one too).
In our area, where ‘Certificate of Continuing Occupancy’ inspection catches such work at the time of sale, the owner eventually will have to retroactively apply for permits and have the work inspected.
Despite the risk, this usually ends up being cheaper than going the permit-in-advance route, mainly because unless something was done grossly wrong, the municipality is mainly interested in doing a pro forma inspection and collecting the cash. So one gains a bit of leverage, as compared to needing (and often waiting for) affirmative permission at every step along the way.
Proposing to build a shipping container home here would be literally laughed out of town. The zeitgeist of the NYC suburbs requires maintaining the illusion of middle class, conformist respectability at all costs. Hippie freaks can move to Oregon or somewhere. /sarc
Ah, the old Conformity gag. Yes, I know it well.
I guess the Little Theatre staging of “We Bombed in New Haven” is out then?
“Effectively there’s a ‘housing guild’ which protects the interests of (first and foremost) local governments and officials, and secondarily licensed contractors.”
Like an iceberg, you’re just seeing the tip, what’s visible.
Local gov and “licensed contractors” (whatever that means) are very small potatoes in the overall scheme of building anything. There are lots of cases where insurance determines design more than code.
Who taking a cut first?
#1 Fuel to get the stuff, and people, to the site of construction, everyday (BIG part of labor cost)
#2 Concrete/cement THE most opaque market in the world is cement
#3 The lumber lobby.(including plywood/RESINS) No building without stamp.
#4 Steel Yeah, they’re still around
#4a fasteners Can’t build without lots of screw
#5 Building supply store/dealer +20%, at least depending on local oligopoly conditions and access to rail transport.
Snotty neighbors and small town politics are probably at about 25 or so on any list I can come up with
Don’t forget that other sacred cow, “property values.” The local bureaucrats are often doing what middle class, conventional homeowners want them to do. I believe this is the biggest driver behind bans on manufactured housing.
Yes when they can, when they can. But I’m not to blind to have noticed how 3rd world this country is getting, maybe not in the top 20% neighborhoods, of course.
One corner of a block I walk daily near work, it’s on the grid a city block with grid laid houses standard suburban/semi-urban architecture, neither the best nor the worst part of town, well there probably is a rotting structure of an original house there once, and then there’s tin covered roofs propped up covering most of the rest of the lot, here’s your favela in the middle of a city block. And then it reeks of the stench of pee whenever you walk by. Homeless in cardboard boxes I expect, homeless villages I have come to expect, whole favelas not under the bridge but right on city block … welcome to the post 2008 world. I do look with some fascination.
Of course without any of that enforcement one cheap way to go about it to me seems to be just put a trailer on someone’s property that owns property (the ‘rents if your young and they’re around, or a friend’s place if your not etc.) but this is mostly enforced against (perhaps not on the block that doesn’t even enforce against the filthy favela! That’s why that’s a wonder to behold, because it’s still not actually normal even in the “new normal”, but it may be a sign of things to come …).
Those pretty shipping container houses in the pictures are expensive architecture using containers as cool industrial design elements. I already spend enough time at work in conex boxes with plywood siding and benches made from 2x4s to want to live in a truly cheap container structure.
I love the picture of a $2,000 container on a $2,000,000 lakefront block, why would somebody bother? As an engineer it seems fairly obvious (to me) that something designed for a purpose will be more efficient and cost effective than something repurposed. I’ve never really understood the fad for using shipping containers, unless you have one lying around and need some extra storage.
As I write this in Singapore I’m looking out at a construction yard with 8 containers stacked to make a site office …. that makes some sense to me as they are modular, they can easily drag them off to the next site and they have all the cranes and trucking handy to move the containers. As the second biggest port in the world, spare containers must be cheap as chips.
Otherwise what’s wrong with a good old fashion prefab portacabin?
I agree with your thought that a shipping container home was akin to a build-your-own trailer home. Repurposing shipping containers does remind me of some of the converted rail car buildings I’ve seen – only practical if one is taking advantage of a surplus to recycle an existing structure acquired for pennies on the dollar.
I could definitely see a future in a modular, pre-fabricated home – and using the shipping container specs for the exterior of each module could have advantages if the idea was to build them in low-cost areas and then transport them via cargo vessel. However, this assumes that long distance transport will remain inexpensive. I’m not sure that is realistic.
An electric mobile home with collapsable solar panels and a 100 mile straight-line travel range (plus a towable gas-powered generator for range extension) would seem more practical. The ability to move easily to a different location has distinct advantages,
Suffer no more the pangs of unrequited housing! Panelfab is here to save you! (Or not. They closed down.)
Panelfab was a Florida corporation situated in North Miami, Florida that manufactured building components designed to be erected and connected in double quick time. A lot of their business was public infrastructure for “underdeveloped” regions: schools, government offices, clinics and the like.
Panelfab:
http://www.corporationwiki.com/Florida/North-Miami/panelfab-international-corporation-2528147.aspx
The uniform sizes and boxy dimensions of shipping containers make them ideal for use in designing innovative, low cost buildings for just about any use. Attaching or stacking containers provides for almost limitless possibilities in terms of office buildings, emergency medical clinics, detached home offices and studio spaces and thousands of other applications.
http://www.buildingpro.com/shipping_container_conversions.html
In the unplanned, unregulated communities that are part of the incredible expansion of urban Kabul, used Chinese shipping containers are one of the building modes of choice. A sign of moving up in the world is adding an extra container to your existing home.
Plus you can toast a few chapatis on the roof at midday.
Oh yes. We self important Westies forget about the “favelas,” to use an appropriate term, that ring about the more conventional city centres. In such circumstances, a conex would be a big improvement over a tin and cardboard shack.
http://www.ihomedecoration.com/3506/photos/how-much-do-shipping-container-homes-cost/
This is really an issue concerning the affordability of decent housing for the teeming multitudes. Now there’s a business idea. Turnkey kits to turn a plain conex into a micro home.
If you’ve ever helped build a Habitat for Humanity home, you know that they already have pre-fab, snap together houses…at least for the framing/walls. The houses arrive in large, pre-insulated panels (basically foam sandwiched between two sheets on ply-wood). Once the foundation is in, it’s literally “insert tab A into slot B…” They go up very quickly compared to other stick-built houses I’ve worked on, and the finished product isn’t too bad…much more gemütlich than a shipping container.
On the whole though, I think I’d still rather live in an earth-bag home.
A friend built one. He was in incredibly good shape by the time the bags were laid.
I have a question, I wonder and am.concerned about left over pollution in these containers. For example heavy metals from broken light bulbs or spilled industrial chemicals. I would love feed back about potential ability to clean the containers and the risk of said spills. Thank you.
CHU or containerized housing units were used as the bunks for troops in both Iraq and Afghanistan. Baths and toilets were generally in separate units. Hookups were standardized and finished on site. They are mobile homes without wheels.
Architecture schools have been exploring CHU since at least the 1990s as efficient mobile office and housing solutions.
I know from personal experience on job sites that the toxic cans issue is never even considered. The rule of thumb is; “You take what we give you and make it work.” I have seen conex cans pressure washed inside and out when bigwigs are expected to come and inspect the job site. (What a laugh! Pure theatre!)
Once a conex is pressure washed, (no one seems to ask about what happens to the gunk once it hits the ground,) the primary ‘toxic’ issue is rust. On most job sites, rust is treated as an old friend. Unless the conex is going to be on site for more than a year, the rust issue is given a shiny new coat of ‘benign neglect.’
I’ve never seen any benefit to using shipping container.
Generally, all of the “budgets” tossed about are with all DIY labor. Free, in the same way as ‘the sharing economy’ is free. This also assumes skill, which is now downloadable via youtube. Thousands of trips to the DIY store are also ‘free’, right travis?
The biggest single factor is building “cost” is shipping/fuel. Building materials are heavy. Containers require big trucks to transport and then big handling equipment to place. This is all after the real heavy equipment has built a base or foundation for it.
Good overall arc with the post.
…all good points. Maybe this discussion should take a look at the Plains Indian Tipi. Light, functional, transportable and locally resourced. (I lived in one in Idaho for a year; superb housing.)
Great article container houses are the coolest, I wish more people would do container homes, but some cities and there building codes are getting in the way.
It’s also the same problem people with tiny houses on wheels some places won’t allow you to live in the tiny house, because of square footage.
I’m sorry to say but, ceramic paints insulating properties are “non-existent”.
http://www.greenbuildingadvisor.com/blogs/dept/musings/insulating-paint-salesman-tripped-his-own-product
Yes, well, I guess the globalist free traders would win the final battle.
Tho the nice rural setting helps a lot. In “Ready Player One”, they stacked trailer homes on top of each other in trailer park high rises next to the city. Peak Oil, ya know, and the trailer park residents needed to take the bus to the city to go on job searches.
While I do not live in a container, I would not rule it out and would have probably explored it more in depth in my earlier years. I do own a quantity of them and use them for storage in my business. One of the principles I try to consider when making plans is maximize and maintain flexibility in my future options. If for some unforeseen reason I had to pack up and move (e.g. I wanted to sell the land or the local government got too owly) I could pick up and move the business with minimum impact. I have the equipment to handle it if needed.
I see the creation of the containers into a living space as more of an adventure and at my advanced age I figure just being in business for myself for the last 35 years was adventure enough. I look for smaller adventures now. As the technology advances in 3D printing I would probably explore that option for quick, efficient, and economic shelter. In the not too distant future you can have a better floor plan complete with utilities printed up and ready for the final touches in a matter of days.
One problem, socially, is the portability of container housing. House trailers are low-scale, vulnerable, and only marginally moveable, not widely approved of. But should modular, portable housing become mainstream, and housing parks become as routine as suburbs, then not only jobs but whole populations would become portable.
What’s the problem with increasing the nomadic nature of America’s citizens? A loss of place, of loyalty to a birthplace, of caring about, or even noticing the degradation of a place. Noticing degradation, or caring about it, is a function of memory, and only generational habitation provides that sort of memory.
Noni
thanks lambert, i love these jointless joints… oh so flexible
Huh?
The whole construction will be dam cold in the winter, all the steel ice cold when it is minus temperature. Some sprayed foam won’t do it. You will get the dew point inside the steel.
Joe Lstiburek told me a few inches of 2 lb/ft^3 spray foam would work for the typical steel building in a northern climate so no reason it wouldn’t work for a shipping container as well.
I think that air flow will have something to do with the condensation issue. These conex boxes can be made very air tight if needed. The ‘product’ in the conex being shipped, which can mean weeks at sea, often needs to be kept dry. The ‘boxes’ were designed with this in mind.
These containers would easily adapt to their best use by digging a hole and dropping them in, making them suitable, insulated by the surrounding earth, not plate glass solar hot boxes. I’m afraid all of the lessons of passive solar home design have gone down the drain with all of the other lessons of the New Age Eco-topian built environment during the morning in America moment and dot.com frenzy. The containers are a good main component to build a Net Zero constructed home, one which produces more energy than it uses. Even without the hole in the ground, surrounding these metal sweat boxes with rammed earth can still provide a well insulated home that could be warmed by the heat of the users and their cooking and other appliances. Steel containers as homes needs to take the next step by internalizing energy production into the zoning and construction specifications.
http://www.zerohomes.org/zero-energy-homes/
Here’s an example of a Net Zero home built 25 years ago. here.
That is a brilliant idea, and works in Maine, too.
http://articles.philly.com/1988-02-28/real_estate/26240917_1_passive-solar-solar-power-solar-designs
Architect BobThomas is referenced in this article over an entire block of new construction row houses built without central heating using passive solar design. The homes have been occupied now for over 25 years and were built as subsidized affordable housing in North Philadelphia. We have had 40 years of notice and warning and more than enough time to have built out many new constructions as homes, offices, warehouses etc with passive solar design. Over 100 million more people since 1974 and the first oil shock. We started and then just ground to a measly nearly all but dead crawl. In the last few years, more has been built using solar energy than in the last few decades. The pace will only accelerate due to the fact that many more people now know the boom bust cycle will continue and to persevere with constructing more solar power, electrical vehicles, no matter what the temporary fluctuations are in crude oil, natgas or other prices. They will go up again, higher than before forcing more and more people to abandon fossil fuels as no more than iron clad taxation that permanently exports money out of local economies, like runaway jobs, never to be seen again. Internalizing energy production locally will stop the financial bleeding, at least for this one commodity. The sooner your region does this, the stronger your community will become over the long haul.
FIRST YORKSHIREMAN: You were lucky. We lived for three months in a paper bag in a septic tank.
Pure luxury – if only I could have lived in an enclosed septic tank in my childhood. W lived in non organic genetically manipulated non measles vaccinated cow “pies” that were in volcanoes in boiling lava…and that was only due to the charity of the Salvation Army at Christmas. All the other months of the year, it was much, much, much worse….
At least your lot had heat! We would save the ‘corpsicles’ from winter and use them to cool the habitat in summer. Gah! Kids don’t know what tough is today.
I remember in the cartoon show “Futurama” when Fry went to the year 3000, and was looking for a place to live. He asked: “Are there still refrigerator boxes?” and Bender replied “Sure, but the rents are atrocious.”
Another advantage: continuous steel walls and ceilings and floors will act as a Faraday Cage, shield out radio waves and prevent the CIA from controlling your thoughts! Although you might have trouble getting cellphone service, and any opening will tend to defeat the effect depending on the frequencies… Also good shielding from lighting strikes, although again, breaks in the wall to let in power and cable etc. will tend to work against that.
Thanks for a refreshing inside-the-box post, Lambert (sorry).
Container homes have novelty appeal, but they don’t have overall structural integrity for truly modular creative flexibility without expensive additional steel framing, and cutting, especially where the 8-foot room dimension is too limiting, which it is for most rooms but bathrooms and closets. The same is true for roof gardens; you’d need additional framing, decking, and failsafe waterproofing. They are value-engineered for specific stacking with heavy end corner frames only and otherwise thin skins over light longitudinal rails. However, at a certain price, if/when global shipping collapses, they just might be practical.
Another consideration for container homes is contextual place-consciousness. Most of the real examples to me stand out like monuments to architectural prowess, stark steel erections that might cause one to seek medical advice. Architects often accentuate the severity of “the box”, as a crisp complement to the setting, and Wright’s “Falling Water” is an exquisite example that works because it explicitly echoes and abstracts the natural rock ledges of its site. But too often modernist structures fail to create such synergy and just seem jarring and domineering.
“Boxy” modular houses can fit their settings, however, if they are not too self-important and a designer gives thoughtful deference to the site and setting in landform, materials, colors, garden architecture (walls, porches, arbors, paving, etc), and vegetation. These can meld site and structure, evoking an inevitable, rooted sense of belonging. It’s really sublime to find those rare examples of built/natural synergy when you cannot envision a site as whole without its human edifice.
So glad that the potential macroeconomic implications of alternative/”austere” domestic architecture is getting attention! I am a graduate student currently writing my dissertation on the adoption of “tiny houses” by homeless activist groups working to establish resident-managed settlements in the US (I work primarily in the Northwest).
It is very true that zoning ordinances and building codes make it extraordinarily difficult to (legally) live in “tiny houses” and similar alternative/DIY forms of domestic architecture. This is the reason why the number of people enthusiastic about “simple living” in such forms of housing far outstrip the number of people who actually do so.
I’m an anthropologist, so my research is not exclusively about the economics involved in the difficulties and obstacles to alternative housing. But I guarantee you that there are a sizeable number of households in America who would jump at the chance to live in such accommodations in order to reduce their monthly living costs. I would love to chat with some economists about the extent to which zoning, building codes, infrastructure requirements, and the cost of engineering and professional certification amounts to rent-inflated housing costs (even apart from land values) across the board (even in publicly subsidized housing).
why would one want a regular looking home built inside an 8 foot wide structure?
side by side looks like bad planning
and having someone else build it for you 100% sounds like an invitation to have
your funds converted to some pints at the office of your local barstool contractor…
zoning is a problem if you are not looking for reason to get it built…
calling it a home is a stretch…it is certainly an ancillary building ripe for co-housing
where one purchases a 99 year lease or some other form of use and occupancy
and get permits for a pool house or garage with loft…so housing can be
worked around…and it helps to build a big fence so your annoying stepfordettes
can’t say that they are not happy with how your space looks to them when they
have nothing better to do…
it is also possible to have some co-housing by using older maybe even derelict
mobile home parks….there are many small unregulated mobile home parks
which would allow for such creative housing situations…in florida, a property with
less than 10 units is an unregulated entity which pretty much would allow any
type of construction one can think of in respect to using containers. One would
need to register the structure as a possible motor vehicle…
and as for difficulty in getting the unit to a location…yes the crane is an issue
perhaps, but one would simply put it on the same type of trailer that it would
be used to drive across a road, so it should not be some mega project.
Much depends on where you are and what you are looking to get done…
but there are dozens of way of making this work without having some giant
costs…
If one were looking to save on expenses, one should source from systems
designed for tight spaces.. mobile homes, rv’s and sailboats/live on boards at the end of
their useful lives should provide possible affordable alternatives for those
not receiving monthly payments to their po box on Dorcy Drive
Ceramic “insulation” has limited applications where it would be considered to contribute much to a complete home insulation package. Pretty good for the firewall on your hotrod though.
Never thought I would disclose personal information on this site but this topic strikes pretty close to one of my means of making a living. I do home building and remodeling on an on and off basis and I have had discussions with people on the topic of shipping container homes. I can’t get past it being another bourgeois-living aesthetic (another one in a long line), but my critique will focus on the problems with construction/manufacturing. I will focus on the issues with structure and design before moving on to the particulars of amenities.
To start, shipping container homes require metal working, and this is far more difficult than work with wood/wood composites/sheet concrete material (I also do metal working as well). Costs in welding, gasses for metal cutting, grinding, etc. The labor will always cost as much if not more than building a small wood framed house and this does not include the cost of obtaining and moving the shipping container (I assume the owner will not just give them away logistics included). In addition, you end up needing to frame the interior of the home with wood anyway.
The lack of wood framing is always going to be an issue. How do you insulate these? There has to be a home envelope otherwise utility costs would be horrendous. Have you ever been in a metal vessel during a hot summer day or a cold winter day? Try it sometime. Metal is a terrible insulator. Then there is the issue of plumbing and electricals. Assuming there is no home envelope. Are the plumbing and electricals exposed? I won’t continue unless asked, there are just too many critiques.
Moving on to a philosophical critique, this is another manifestation of Green Capitalism amongst the privileged. It is ironic that the excrement of Capitalism’s excesses, the shipping container, is being “repurposed” for home building. Rather than question the structure lets just reuse the junk. Better than nothing I suppose, but as I already said, not efficient and not economical in terms of energy and labor. Unfortunately for the shipping container home fad, you can build a 500 square foot home much faster, and much cheaper, using spruce-pine-fir wood (which is far more environmentally friendly than the process that manufactures large steel shipping containers) and high quality, modern sheeting and roofing materials (concrete sheeting/exterior and standing seam roofs). Include good insulation, usually one of the largest expenses in small square footage homes, with efficient heating (hot water) and a window unit and you have a fairly inexpensive home that is very energy efficient. Though I’m sure the trend will make some connected, hip developers very wealthy in the coming years.
Very insightful. More “suitable” repurposing of containers might be prisons, extraordinary rendition, and of course, enhanced interrogation. Apparently, the CIA is already ahead of the curve on this. Containers were used at Bagram as holding cells, for prisoner transport, and other creative purposes. (Sorry, Lambert, they’re not bullet-proof.)
http://news.bbc.co.uk/2/hi/8147383.stm
A number of years ago my law firm was involved in a shipping company bankruptcy. The company owned or leased tens of thousands of containers, and couldn’t find thousands of them. It turned out that a large number of the missing containers had been turned into housing throughout the developing world.
A local logistics company, GCD Glomb Container Dienst GmbH, had a problem with people not returning their shipping containers, so, they surveyed the colors in use and repainted theirs a unique, bright pink, to make them easy to spot. I wonder if that color has become less helpful.
From my architecture bookmarks,
Lustron Homs from the 50’s, Prefab enamled steel. These were an EFFICIENT use of resources, ahead of their time, or actually appropriate for their time and appropriate again. I visited a friend’s friend Lustron, actually a couple of them integrated together on her property and outfitted exclusively w/ 1950 appointments. A mindblower time warp inside. The kitchen is like an appliance museum. OK, she’s pretty eccentric but these things really very energy efficient, built kinda like an oversized insulated cooler, can be erected and enclosed in a day, w/very precise “joinery”
http://www.lustron.org/film.htm
http://www.lustronpreservation.org/
I agree w/ comments above, even if the intermodal shipping containers are free stranded assets, probably still not too efficient of a place to start for building a home when considering the whole cost. Interesting possibilities none the less for a rural environment cottage or more obviously as storage. I have friends in Chicago that have a two flat repurposed as a hobby man-cave –they keep the winemaking kit in a intermodal container hidden (screened) in the back yard. They have a ubiquitous Chicago alley and must have placed it with a telehander or yard truck (bigass forktruck).Fantastic for what it is.
Another link http://containerspace.tumblr.com/
reflecting comments above, nonetheless, some intersing design exercises
The Pros and Cons of Cargo Container Architecture
On Arch Daily, Brian Pagnotta mentioned a few often overlooked potential cons of container housing. Jetson Green summarizes his article as such:
Con #1: Toxic Paint Coatings
“The coatings used to make the containers durable for ocean transport also happen to contain a number of harmful chemicals, such as chromate, phosphorous, and lead-based paints.”
Con #2: Toxic Wood Floors
“Wood floors that line the majority of shipping container buildings are infused with hazardous chemical pesticides like arsenic and chromium to keep pests away.”
Con #3: Upcycle Energy
“The entire structure needs to be sandblasted bare, floors need to be replaced, and openings need to be cut with a torch or fireman’s saw.”
Con #4: Ecological Footprint
“The fossil fuels required to move the container into place with heavy machinery contribute significantly to its ecological footprint.”
Con #5: Awkward Spaces
“Taking into account added insulation, you have a long narrow box with less than eight foot ceiling. To make an adequate sized space, multiple boxes need to be combined.”
Con #6: Opportunity Cost
“In many areas, it is cheaper and less energy to build a similarly scaled structure using wood framing.”
Steve from Tin Can Cabin also has a few thoughts on pros and cons of container homes.
What do you think?
I don’t want to live in a fucking Tiny House. I don’t want to live in a fucking Shipping Container. I want to live in a standard normal house!
I hear you Pepsi. However, Phyl and I have met numbers of people through the years who had nothing to live in. We lived in a tent for a while. Then an old Airstream travel trailer. When you have to, you can live small, and even enjoy it.
The original “Four Yorkshiremen” sketch was performed and written by the cast of “At Last the 1948 Show” with Tim Brooke-Taylor, Marty Feldman, John Cleese and GrahamChapman. Only later two went on to be members of the Monty Python team.
http://youtu.be/DAtSw3daGoo
A ‘village’ of containers was one solution chosen to the housing shortage for Dutch students, here’s an english language website : http://www.tempohousing.com/projects/keetwonen.html
I’d prefer the log-cabin.
“Demand destruction” – I was thinking of “demand destruction” in terms of all the consumer crap packed into those shipping containers. If shipping containers are freeing up en masse, then there must be decreasing demand for the landfill-destined products that go in them.
I think this is a sweat pictures for Home Shipping Container too